製造工程Process
グミが出来上がるまでの製造工程を簡単にご紹介
グミ仕込み、START!
さぁ、これから「グミ」を作って行きますよー!!
まずは、身支度から。徹底した衛生管理を行っていますので、チリやホコリを持ち込まないよう、入口で入念にチェックしてから工場内へ。
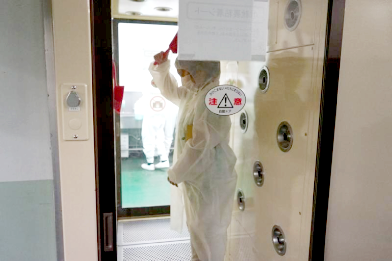
原料の確認 → 計量
なにごとも最初が肝心!まずは、原料の確認を入念に行います。
入荷数量・梱包形態(破損・汚れ等がないか)、保存場所や品質保持期限は守られているかなど、細かくチェックし、OKならば計量作業へGO!ロット№、品質保持期限を確認し、異物等が混入していないかを開梱して確認します。
さらに計量器も動作確認をしてから、レシピ通りにキッチリ計量! グミの食感は原材料の配合がキモになりますから、ここは慎重に。
準備ができたら、いよいよ大鍋に原材料を投入します!
溶解混合
「溶解混合」とは、材料を混ぜながら溶かしていくこと。
水飴等を投入後、撹拌しながら加温していきます。溶液が沸騰したら、糖を投入します。
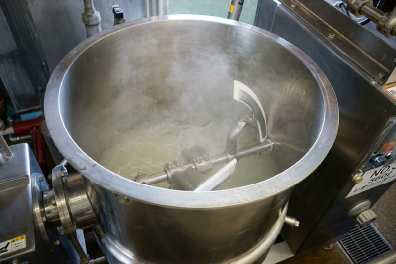
減圧濃縮
どんどん煮詰めていき、溶液の重量をチェックして行きます。
規定値になったらBxを確認。まだ規定値に満たない場合は、再び煮詰めて濃縮させます。重量の変化はチェック表にしっかり記入。
その後加温して、みんなでグミ原液の仕上がり具合を見守っていきます。
膨潤溶解
必要に応じて消泡剤を投入した後、いよいよ“固める”お役目「ゼラチン」の登場です。
ゼラチンも他の材料と同じように、まずはロット№、品質保持期限、梱包形態に破損や汚れ等がないかを確認します。同時に、計量器が正しく動作するかもチェックします。
すべてクリアしたら、ゼラチンをまんべんなく水に馴染ませて溶かしていきます。
よーく混ざるように、かき混ぜて・・・
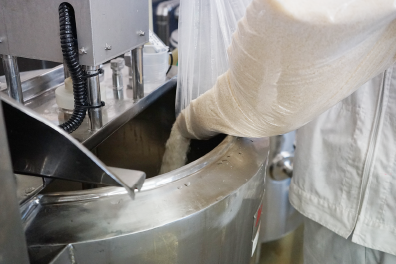
添加物計量 → 混合
グミの味に合わせて、色付けをしていきます。添加物も他の原材料と同様、しっかりと事前チェックをしてから計量し、チェック表にサインしていきます。
色素は溶けにくく、直接入れるとダマになったり、色の濃淡ができたりするので、事前によく溶かしてから投入していきます。投入する順序も大切なので、「仕込原料投入管理表」の投入順序に従って、作業を進めます。
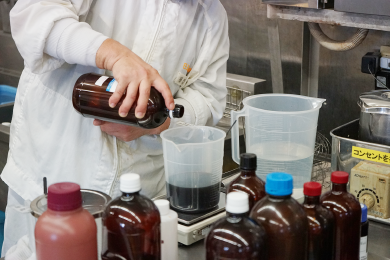
ブリックス(Bx、糖度)調製 → 送液
Bxを確認します。確認できたら、ストレージタンクへ送液します。このとき、移送中に液体が冷めないよう、配管も温めておきます。規格Bxでない場合は、加水にて調整してから液を送ります。
加水した量は、もちろんチェック表に記入し、万全な体勢でグミ液を送り出します。
保温
ストレージタンクの中で、グミたちがぬくぬくとお休みできるように、温水設定温度を確認します。
仕込み作業は以上です。続いて「充填」の工程へと進みます。
トレー搬入 → スターチ充填 → 型押し
トレーに敷き詰められている白い粉はコーンスターチです。
いろんな形が手軽に作れる上に、コーンスターチ自体が食品なので、とっても安全です。型が最後まで押されているかどうか、確認します。
グミ、充填!
充填機にトレイをセット!いよいよグミを型めがけて充填していきます!
ここでのポイントは、グミ溶液の温度、液漏れがないか、気泡が混入してないか、などです。
すべての充填条件設定をクリアしたら、トレーの中へ!
充填完了! → 乾燥
充填完了!
グミがキレイに型に入りました!
充填したてのグミは、まだ液状なので、これから専用の乾燥室で2〜4日、乾燥させます。グミを搬入する前に、乾燥室の温度を確認し、送風扇のスイッチオン!
グミが固まるまで、しばしのお別れ。グミちゃんたち、ゆっくりお休みください。固まったらまた会いましょう!
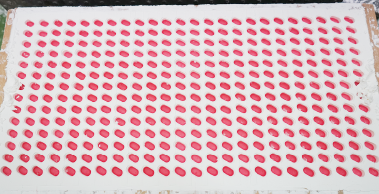
グミとの再会(デモールド)
規定の日数が過ぎグミが乾燥したら、グミのトレーを乾燥室から運び出します。
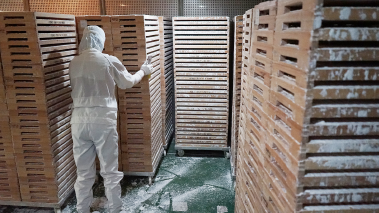
スターチ除去
まずはトレーに敷き詰められているコーンスターチを除去し、トレーからグミを取り出します。
コーティング
オイルやオブラートなどで、グミをコーティングしていきます。まんべんなく噴霧されているかが、チェックポイントです。
選別
変形、双子、へこみ、テーリングなど、製品として出せないグミはここで取り出し、廃棄します。
金属検出
続いて金属片が混入していないか、検査機を使ってチェックしていきます。
検査機は始動前に鉄(Fe)やステンレス(SUS)のテストピースを使い、正常に作動するかを確認した上で動かしています。
この検査で排除された製品については、必ず再検査を行い、異常が見られなくても全て廃棄します。また、異常品は品質管理室へ提出し、今後の対策のデータとします。
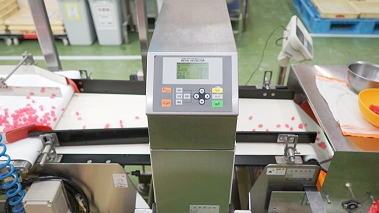
キレイなグミができました!
グミの完成です!
このあとは、[計測]→[商品パッケージに詰める]→[ダンボールに梱包]→[配送]という流れになります。
どんな製品を作っているのかネタバレになってしまうので、写真の掲載はご勘弁願います。
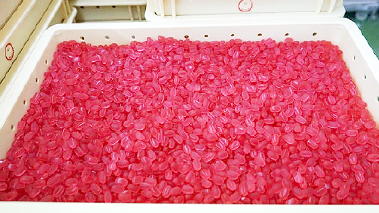